Paradox: Grüner Beton?
Beton – dieses Wort klingt wie der ›Sündenfall‹ selbst in der Architektur. Doch längst gibt es viele beeindruckende Beispiele, dass Beton nicht gleich Beton ist. THE PROPERTY über die Wandelbarkeit eines Baustoffs.
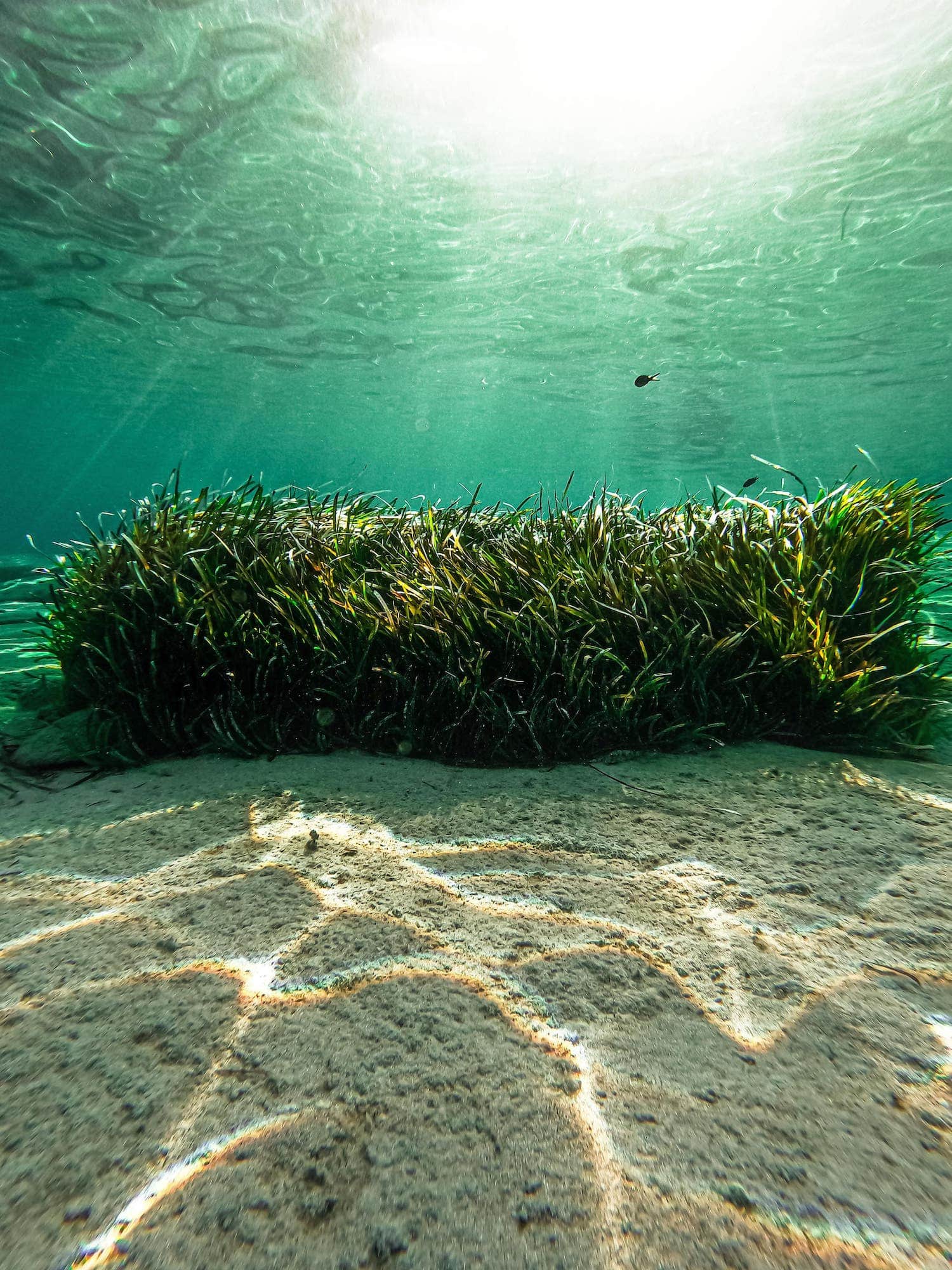
Foto: Alexandros Giannakakis
Man hat den Beton in den vergangenen Jahren nicht unbedingt geliebt. Als ›Klimakiller‹ oder gar ›Klimabombe‹ hat man ihn bezeichnet. Ganz abwegig ist das nicht, denn bei der Produktion von Zement, dem wichtigsten Bestandteil von Beton, wird viel Kohlen-
stoffdioxid freigesetzt. Insgesamt würde die Beton-Herstellung rund fünf bis sogar zehn Prozent zum weltweiten CO2-Ausstoß beitragen, heißt es.
Doch ginge es auch ohne? Schließlich sollten alle, die schimpfen, auch in Alternativen denken! Wie also ließe sich Beton umweltfreundlicher machen?
»Es gibt viele Rädchen, an denen man drehen kann«, antwortete 2018 der Baustofftechnologe und Betontechnik-Experte Björn Siebert von der TH Köln. »Beton ist ein Vielstoffgemisch, das aus diversen Zutaten besteht. Deshalb gibt es auch verschiedene Wege, ihn umweltfreundlicher zu machen.« Heute schon gibt es vielerlei Zusätze, die man beimischen kann, um dem Beton ganz besondere Eigenschaften zu verleihen. So lässt sich zum Beispiel hochfester Beton herstellen, der viel belastbarer ist. »Damit können Sie Betonwände dünner dimensionieren, die genauso tragfähig sind wie herkömmliche Wände«, erläutert Siebert. »Wenn Sie die Wanddicke von 30 auf 20 Zentimeter reduzieren, ist die Betonersparnis beachtlich.«
man, um mächtige Stahlbetonteile für den Haus- oder Brückenbau filigraner zu machen, auf den Werkstoff Carbon statt Stahl gesetzt. Da Beton zwar hohen Druck ertragen kann, aber empfindlich ist, wenn man an ihm zieht, ergänzt Carbon den Werkstoff ideal. Bauteile wie Brücken oder Geschossdecken stattet man deshalb bereits zusätzlich mit Stahlmatten aus, die Zugkräfte leichter wegstecken.
Carbon und Beton als ideale Partner?
In einem weiteren neuen Forschungsprojekt integrieren Forscherinnen und Forscher am Institut für Betonbau an der HTWK Leipzig Carbonbeton-Bauteile auf Basis des industriellen Kommunikationsstandards AS-Interface. Folgt man der Argumentation von Prof. Dr.-Ing. Klaus Holschemacher, dann haben Häuser aus Carbonbeton sehr schmale Wände; viel Platz für die zahlreichen Installationsleitungen, die sonst darin verbaut werden, bleibt nicht. Leitungen, Kabelkanäle und Schaltkästen sollten deshalb schon in der Bau- und Installationsphase reduziert werden.
Warum nicht einfach recyceln?
Energie, Kohlenstoffdioxid und Rohstoffe ließen sich auch einsparen, wenn künftig die Substanz alter Gebäude besser genützt würde – in Form von sogenanntem Recycling-Beton. Er entsteht, wenn Beton aus Abbruchhäusern zerkleinert und frischem Beton
als Gesteinskörnung beigemischt wird. So benötigt man weniger Sande, die man in Kiesgruben und Flüssen ausbaggert, oder natürliches Gestein, das man in Steinbrüchen aus dem Fels sprengt. Zudem spart man sich den langen Transport zum Betonwerk. Das ist vor allem in Großstädten sinnvoll. In der Theorie ließe sich der Abbruch aus einem Gebäude gleich auf der nächsten Baustelle wiederverwenden.
Doch dass die Deutschen beim ›R-Beton‹ so zurückhaltend sind, hat seinen Grund. Mischt man frischem Beton Altbeton bei, wird es aufwendiger, eine konstante Qualität sicherzustellen. »Haften an der Gesteinskörnung des Altbetons noch Reste von altem Zement, kann das dazu führen, dass der Beton mehr Wasser zieht«, erklärt Beton-Experte Siebert: »Von Beton-Charge zu Beton-Charge können die Eigenschaften mehr oder weniger stark schwanken. Das kann problematisch sein, wenn man große Teile betoniert, die eine gleichmäßige Qualität aufweisen sollen.«
Echte Alternative zu Beton aus Algen?
Gänzlich ohne Beton kommt ein Bauverfahren aus, das Thomas Brück, Professor für Synthetische Biotechnologie an der TU München, gemeinsam mit dem Münchner Start-up ›TechnoCarbon‹ entwickelt hat. Es nutzt natürlichen Granit, den ein Wasserstrahlschneider in Scheiben von wenigen Millimetern bis einigen
Zentimetern zerlegt. Diese Lagen werden wiederum mit dünnen Schichten aus Carbonfasern verklebt. Durch die Verbindung von druckfestem Naturstein mit zugfesten Fasern entsteht ein Material, das nach Angaben von TechnoCarbon eine höhere Festigkeit und Dichte als Metall aufweist. Die Elastizität (›E-Modul‹) lasse sich »in weiten Grenzen« durch Faserrichtung und -stärke einstellen, und zwar im Bereich zwischen Aluminium und härtestem Stahl. Die Carbonfasern können umweltfreundlich aus Salzwasseralgen gewonnen werden, die in Bioreaktoren gehalten und mit Kohlendioxid gefüttert werden – etwa aus einer Brauerei. In einer raffinierten Prozesskaskade, die Brück mit seinem Team entwickelt hat, wird aus den Algen zunächst unter anderem Glycerin gewonnen, aus dem sich Polyacrylnitril herstellen lässt – ein Vorläufer klassischer Carbonfasern. Da nur sehr dünne Faserschichten benötigt würden und der Granit selbst günstig sei, sei das fertige Produkt potenziell schon recht preiswert. »Im aktuellen Stadium sind wir allerdings noch nicht kompetitiv«, räumt Brück ein. Derzeit werden die Algen im Labor in einem 500-Liter-Kessel gehalten. Die Partner suchen noch nach Investoren für einen Niedrigenergiehaus-Prototyp.
PS: Wer allerdings heute schon nach ›Grünem Beton‹ googelt, erhält innerhalb von 0,41 Sekunden bereits 5.630.000 Treffer. Offensichtlich ist es ein Thema, in das es sich zu investieren lohnt.